
Thu August 12, 2021
CEG
Agresource Inc., a Mass.-based corporation, has been doing business since 1984. It supplies services to municipal, industrial and commercial clients throughout the region by making compost from organic materials of many different varieties, including yard waste, food waste and other organic materials and making a variety of products, including compost and custom engineered soils.
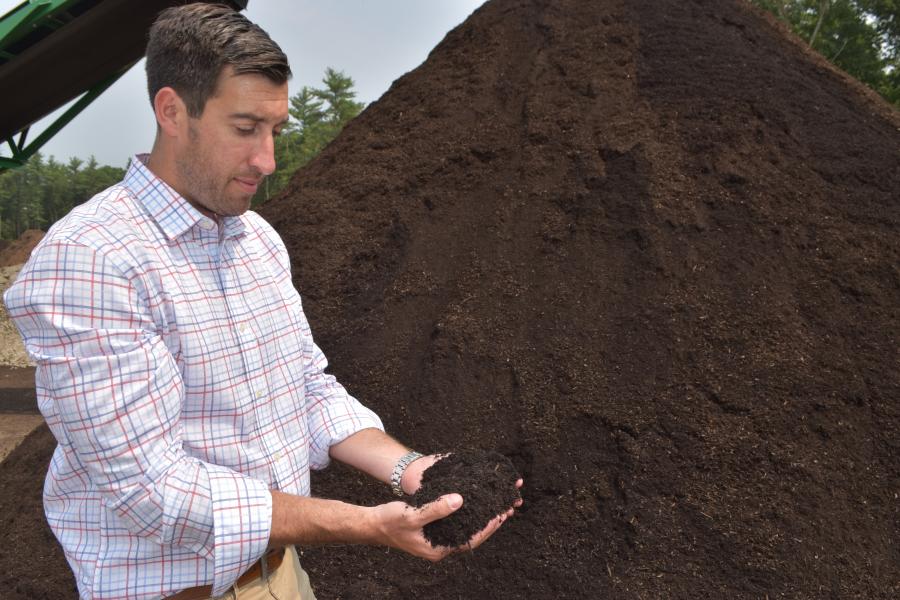
David Harding joined the company in 2012 with a background in the custom soils and composting industry and in 2015 he assumed the role of company president. Under his leadership, the company has continued to have tremendous growth, particularly in product sales of engineered soils and compost. Today, the company has grown to more than 25 employees and experiences double-digit sales growth each year.
According to Harding, producing engineered soils is essentially mixing the right combination of base soil, compost and sand to create a soil for a very specific application. For example, Agresource makes golf and sports field soil that is manufactured for high performance, allowing them to drain quickly and not compact; a bioretention soil that is designed to slowly infiltrate stormwater runoff as to not overwhelm the groundwater system while collecting pollutants; a wetland soil, which is specifically engineered to support wetlands vegetation and mimic natural environments, and blending lightweight soils that are designed for rooftop gardens, which have become a staple of environmentally conscious construction trends in metropolitan areas and beyond.
In addition, Agresource has a team of experts who can custom-engineer the soil blend to specifically achieve the goals customers are looking to meet.
Agresource sells its custom-made soils all across New England to a variety of customers that include golf courses, landscapers, contractors, supply yards and garden centers. Agresource has a fleet of trucks and trailers that allows it to deliver to customers throughout the New England area.
Mixing soils, in particular any soil that has an element of compost involved, is uniquely challenging because of its potential moisture content.
"Trying to blend the ingredients that we use by using traditionally vibratory screens would be frustrating and not particularly effective because of clogging issues and a tendency of the materials to not mix very well," Harding said.
Agresource has turned to Rock and Recycling Equipment of Sutton, Mass., and McCloskey trommel screens to tackle the challenges of its soil blending business.
"Over the years, we have found that Rock and Recycling Equipment has been a great partner in helping us match the right equipment to our production needs," Harding said.

According to Shane Fleming, co-owner of Rock and Recycling Equipment LLC, "A trommel screen is really ideally suited for mixing and screening moist materials such as the compost ingredients that Agresource deals with on a daily basis. The tumbling motion of a trommel not only does a great job of mixing the ingredients together, but it also dries and fluffs the materials, which is ideal in this situation.
"Without the material rotating through the length of the trommel. it is unlikely that David [Harding] and his team would be able to reach the tight specs that they are looking for. Depending on the product they are making, they are screening materials from ¾ of an inch all the way down to ¼", which would be virtually impossible using any other screening method."
To reach their ever-increasing production goals, Agresource has purchased six McCloskey trommel screening units from Rock and Recycling Equipment — four model 621 trommels and two model 516 trommels.
The model number clearly describes the size of the trommel screen. For example, on a model 516, the 5 designates the diameter of the trommel, which is much like a giant cylinder of an automatic clothes dryer. The diameter is 5 ft. wide. The 16 designates the length of the trommel, 16-ft. long. So, materials enter the hopper of the trommel screener and are mixed inside a perforated cylinder that is 5 ft. wide and 16 ft. long, until those materials are blended to the proper consistency.
A model 621 does exactly the same job, except the diameter of the trommel is 6 ft. and the length is 21 ft. In either model, there is a conveyor at each end of the unit — one conveyor to discharge oversized, unscreenable materials and the other conveyor to discharge the finished product.
Another aspect of Agresource's business is doing custom onsite compost and soil screening on a contract basis. Agresource operators and equipment are used to prepare specialized soil mixes at construction sites including sand-based root-zone mixes for athletic fields that demand the mix meet very exacting specifications for organic matter content and soil physical texture.
According to Harding, there are a number of reasons that Agresource has exclusively purchased McCloskey equipment for the screening aspects of its operations.
"Mike Lanchanski was my first contact with McCloskey screening plants. Agresource had relied on their trommel screens for years and I quickly understood why. Mike was instrumental in helping us match up their equipment with our growth model to help us be successful. McCloskey and Rock and recycle became a valuable asset to our business.
"As our relationship has matured, I can think of countless times that Rock and Recycling has gotten us out of a difficult situation or has gone the extra mile for us. We had a situation where we had contamination in our finished product. Our mechanics and operators searched the entire plant and couldn't find the source. We got on the phone with Brendan Fox, co-owner, and in very little time he was able to identify the problem and talk us though the solution over the phone. His years of experience are invaluable when it comes to operating these machines most efficiently."

"There was another instance where we had a section of ¼-inch screen fail. It was in mid-September, our busiest time of the year. We called Rock and Recycling at 5 p.m. They went to work and by 6 a.m. the next day, they had created a custom repair, had it in our yard and had us up and running. That is the type of service that keeps you very loyal to a vendor.
"Rock and Recycling is also very good at training our operators on their equipment and getting them knowledgeable enough in the equipment they operate that we are not totally dependent on Rock and Recycling for every little hiccup that comes our way. I cannot emphasize enough that when we do need them, they pick up the phone, they listen, they respond quickly and overall, they make us a productive company.
"We make a very high-quality product that's custom engineered to meet the needs of our customers," Harding added. "It's not a product that we can sell on the basis of price and that is exactly what I appreciate about doing business with Rock and Recycling. They don't sell on the basis of price; they present value and return on investment."
For more information, visit www.rockandrecycling.com and www.agresourceinc.com. CEG