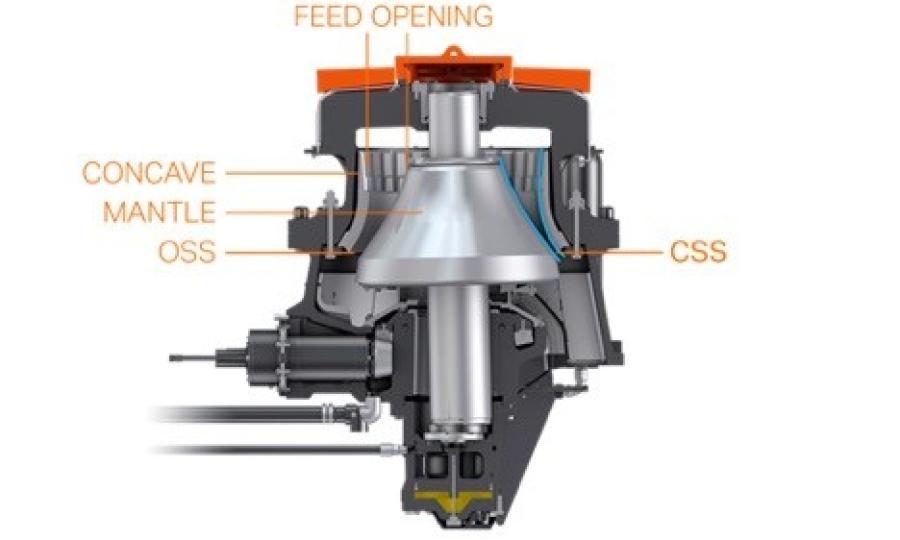
Wed June 03, 2020
Aggregate Equipment Guide
In this Cone Crusher article we want to educate you about what to consider when purchasing a cone crusher. It also will inform and educate you if you are a current owner or operator of a Cone Crusher. If you have a good base of knowledge about cone crushers you can skip through the article by choosing the topics below.
We will be exploring in more detail the following:
- Cone Crusher Manufacturers
- How Does a Cone Crusher Work?
- Cone Crusher Advantages and Disadvantages
- Cone Crusher vs. Jaw Crusher
- How to Adjust a Cone Crusher
- Cone Crusher Diagram
Choosing the Right Cone Crusher for Your Quarry and Mining Operations
Cone crushers are among the most versatile and useful pieces of aggregate crushing equipment with many of these machines playing an integral role in delivering aggregate products to the marketplace.
While cone crushers are a specialized piece of equipment, there are plenty of manufacturers offering high-quality options. That fact sometimes makes it difficult to narrow the field and select the best cone crusher for your business.
Today, we're going to take a closer look at different cone crusher manufacturers so you can narrow the field and select the best equipment for your business.
Leading Cone Crusher Manufacturers
Sandvik
Since 1942, Sandvik has been producing tools and equipment to meet the needs of a wide variety of industries, including aggregate, mining, sand and gravel, concrete and many more. Sandvik's products are available in more than 150 countries, and they employ nearly 8,000 employees worldwide.
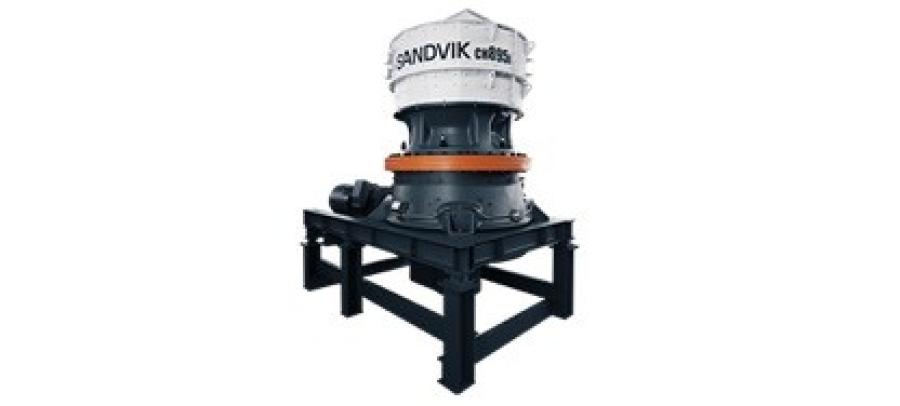
Sandvik is dedicated to sharing its expertise and knowledge with customers and trade organizations in the interest of developing new and innovative products. Sandvik is a member of the Advanced Manufacturing Research Centre with Boeing, Rolls-Royce and the University of Sheffield. The company also has partnered with the Commonwealth Center for Advanced Manufacturing.
Today, Sandvik manufactures nearly 20 different cone crushers, in addition to a variety of other products, including impact, jaw and hybrid crushers.
According to Sandvik, its dedicated sales team is incredibly well versed in their technologies to aid companies that might be uncertain which model is best suited for them. As a result, producers can consult with a sale team member to receive expert advice on the best cone crusher for their needs.
Metso
Metso has an incredibly storied history and well over 100 years of experience in the industries it serves. Metso was founded in 1868 as Sunds Bruk Ironworks in Sweden. By 1918, the company had developed its first piece of mobile crushing equipment, and since then, it has continued to innovate across a variety of business verticals, especially the mining and aggregate industries.
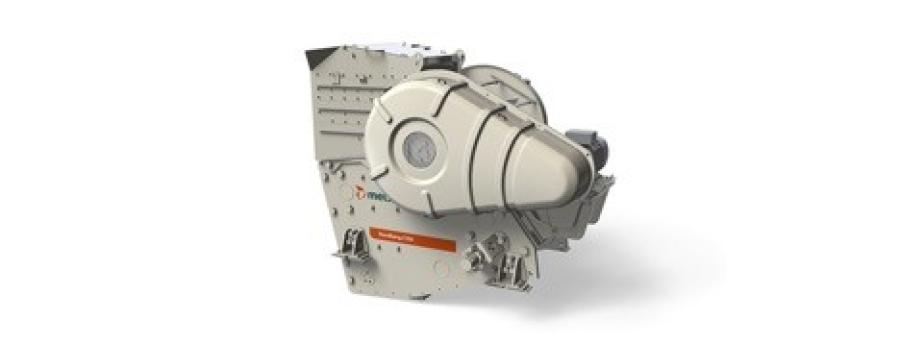
Today, Metso produces four different series of cone crushers, including the Nordberg GP, HP and MP series, as well as the small and portable Metso MX series. All told the brand manufacturers well over 20 different cone crushers.
According to Metso, the manufacturer endeavors to separate itself from its competitors through service and support. Metso provides companies with dedicated maintenance and support services to keep equipment running in top shape for many years to come.
Powerscreen

Powerscreen is a subsidiary of the Terex brand, which was originally developed by the General Motors company to manufacture and sell heavy machinery for the construction industries. It later spun off the Powerscreen brand, and in the time since, Powerscreen has solidified itself as a major player in the aggregate and mining industries.
Today, the brand manufacturers six different mobile cone crushers under its Maxtrak product line. Powerscreen specializes in large crushers, making them ideal for the demands of the mining and aggregate industries.
Powerscreen's cone crushers are all equipped with AutoMax technology, which provides an excellently shaped product in less time, which allows companies to easily scale up their production, according to the company.
KPI-JCI
A heavy machinery powerhouse, KPI-JCI manufacturers a broad range of products to serve the needs of a variety of businesses. It manufactures several different cone crushers under its Kodiak Plus brand name.
All told, there are five different Kodiak Plus cone crushers, with throughputs ranging from 385 to 830 tons per hour. These crushers employ Kodiak's unique roller bearing system, which can help reduce operating costs by an eyebrow-raising 50 percent.
Kleemann
Part of the Wirtgen Group, Kleemann produces a line of mobile cone crushers called MOBICONE. The company's cone crushers are ideally suited to process medium-hard to hard and abrasive natural rock. When linked with primary crushers and screening plants, the MOBICONE delivers excellent cubic final grains in the secondary and tertiary crushing stages, according to the manufacturer.
Kleemann MOBICONE cone crusher models include: MCO 9i EVO, MCO 9 Si EVO,
MCO 11i PRO, MCO 11 S, MCO 13 and MCO 13 S.
Cedarapids

Another subsidiary of the Terex brand, Cedarapids, was initially founded as the Iowa Manufacturing Company in 1923. The company was later acquired by the Terex brand in 1999, and it has continued to produce industry-leading crushing equipment since then.
Today, Cedarapids manufactures five different lines of cone crushers, offering nearly 20 crushers. Cedarapids is popular among companies that demand incredibly high production from their equipment, and its TG1020 crusher boasts a powerful 1,006-hp. motor with an impressive throughput of over 2,500 tons per hour, according to the company.
Terex Finlay
Today, Terex owns several of the most popular equipment companies on the market, including Cedarapids and Powerscreen. While the parent company is well known for these brands, it also manufactures many capable crushers under its Terex-Finlay brand.
Today, Terex makes nine different mobile cone crushers that are well-loved for their high production and excellent product shape. These heavy-duty crushers are ideal for businesses that process large pieces of raw material, as they feature larger openings that are able to process more material at once.
McCloskey
As a subsidiary of the Metco Corporation, McCloskey has been a leader in the crushing and screening industry since it was incorporated in 1985. Today, it makes a broad range of crushers, screeners, feeders and more for use by the mining, aggregate and construction industries.
McCloskey makes five different cone crushers under its C line, as well as several other styles of crusher.The C line of tracked crushers features Volvo Penta engines that provide the high horsepower necessary to make quick work of all crushing tasks. The open chassis design of McCloskey crushers makes them some of the easiest to maintain crushers on the market, according to the company.
Telsmith

Originally incorporated as the Smith & Post company, Telsmith has been serving the construction, mining, and aggregate industries for more than 100 years. Today, Telsmith is one of the most trusted names in the business, and it offers a full line of specialty equipment designed for mining and aggregate industries.
Telsmith makes the Titan, SBX, and SBS line of cone crushers, which are well suited for a variety of uses. Its popular Titan line offers a throughput of up to 840 tons per hour, and it's also compatible with Telesmith's Trac10 automation system, which allows you to operate your equipment with greater ease, safety, and output.
Equipment for Sale From Top Cone Crusher Manufacturers
If you're ready to move forward with a piece of equipment from a top cone crusher manufacturer, use the links below to begin your search.
● Sandvic Cone Crusher For Sale
● Powerscreen Cone Crusher For Sale
● KPI-JCI Cone Crusher For Sale
● Cedarapids Cone Crusher For Sale
● McCloskey Cone Crusher For Sale
● Telsmith Cone Crusher For Sale
● Kleemann Cone Crusher For Sale
How Does a Cone Crusher Work?
Cone crushers are one of the most popular and well-used pieces of equipment that industries like mining, aggregate and more rely on each day. While these massive pieces of equipment can seem intimidating at first, they're quite easy to understand.
So, if you're wondering "how does a cone crusher work?", read on and learn how these massive machines get the job done.
What is Crushing Equipment?
Crushing equipment is used by a wide variety of industries to refine raw materials to a more manageable size. Here are just a few of the industries that rely on crushing equipment.
● Mining
● Rock quarries
● Mineral processing
● Recycling
● Sand & Gravel
● Building materials
Once a company has mined or collected raw material, it must be broken down into a smaller form that more closely resembles the end product they'll be selling. Crushers are typically the first step in the refining process.
Crushing equipment is usually one part of a more extensive system or plant for material handling. Rock crushers, like the cone crushers we'll be discussing in just a moment, generate incredible force to break raw material into smaller pieces. Once material exits the crusher, the user can refine it further to arrive at the final size.
Depending on the application, crushers can be portable and small, exceptionally large, or anywhere in between. Rock crushers are usually part of a more extensive system that includes screeners and conveyors that bring raw material to the crusher.
What is a Cone Crusher?
Cone crushers are one of the most popular types of rock crushers, and a variety of different industries rely on them. Cone crushers are relatively simple machines, and they only have a few moving parts. This is one of the reasons for their popularity since they're easy to maintain and less prone to breaking down than other more complicated pieces of crushing equipment.
Cone crushers are especially prevalent within these industries.
● Aggregate
● Coal mining
● Concrete
● Frac sand
● Mining
How Does a Cone Crusher Work?
Cone crushers are straightforward pieces of equipment, which makes it easy to understand.
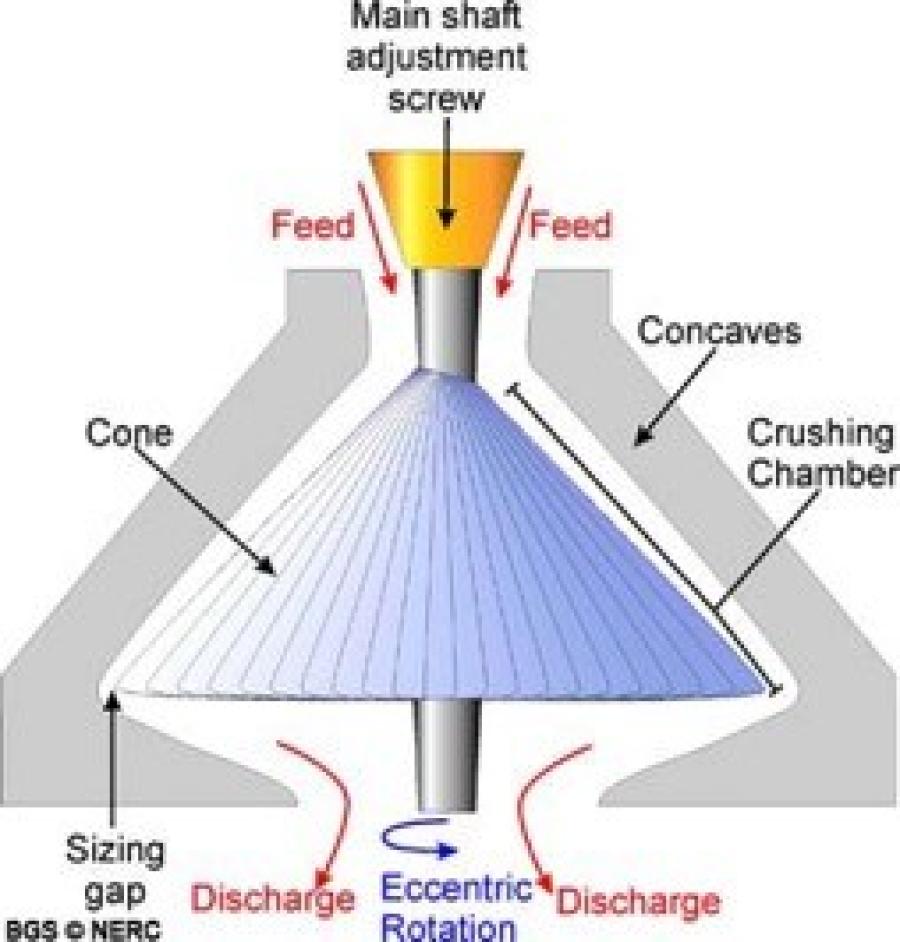
It all starts with the material you need to crush, which is known as the feed. The feed drops into the crushing chamber, which is a large circular opening at the top of a cone crusher. Inside the crusher, a moving part which is known as the mantle gyrates inside the machine.
The mantle moves eccentrically, which means that it doesn't travel in a perfect circle. The mantle can swing slightly while it rotates, which continuously alters the gap between the mantle and the concave.
The concave is a fixed ring that's outside of the mantle. As the mantle swings, it crushes the material against the concave. Stones are crushed against each other, which breaks it down further. This concept is known as interparticle crushing.
The Sides of the Crusher
A cone crusher has two sides: an open side and a closed side. As the material crushes, the particles that are small enough to fit through the open side fall through the space between the mantle and the concave.
As the mantle gyrates, it creates a narrow point and a wide point. The distance on the wide side is known as the OSS or open side setting, while the narrowest point is called the CSS, or closed side setting.
Depending on how the OSS is set, it will determine the size of the particles as they exit the crusher. Meanwhile, since the CSS represents the shortest distance between the concave and the mantle, this is the final crushing zone. How the user configures the CSS is critical for determining capacity, energy consumption and final product size.
The Symons Principle
Many cone crusher manufacturers use the Symons Principle to produce more powerful and efficient crushers.
Based on this principle, each rotation of the mantle is timed in a way so that the thrust of the mantle meets the feed material at the point of maximum impact.
By ensuring that the crusher meets the material at the moment of highest impact, the closing head catches falling material and crushes it while the other side of the chamber can allow material to freely exit the chamber, or fall to the next point of impact.
This premise allows manufacturers to produce cone crushers that enable the user to increase production while also reducing the amount of energy the crusher requires to run.
The Importance of Sampling
The size of the feed is a critical consideration that can affect virtually every aspect of the crushing process. Knowing the size distribution of your raw material will help you produce a more consistent final product while maximizing productivity and reducing undue wear to the crusher.
It's essential to sample throughout the crushing process so you can ensure that the crusher can maintain an optimal level of productivity. Sampling becomes especially crucial if there are any changes in upstream processes that may affect feed size or distribution.
Limitations of Cone Crushers
While cone crushers are quite versatile, as evidenced by the number of industries that rely on them, they do have one inherent drawback. The size of their feed opening limits cone crushers. So, while they're well-suited to crushing a variety of different materials, they're unable to crush material that's too large to fit through the feed opening.
For this reason, companies typically deploy cone crushers as part of a more extensive system of crushing equipment. A first-stage crusher, such as an impact or jaw crusher is used to break raw material down to a size that the cone crusher can accommodate.
Cone crushers are typically looked at as a secondary or tertiary stage of crushing. But, they can also act as the first stage provided the material is small enough to fit through the feed opening.
While these crushers are well adapted to a variety of materials, they don't perform well with moist or viscous materials, such as clay or shale. Highly viscous materials will need to be processed by a different piece of equipment since they can jam a cone crusher.
Cone Crusher Advantages and Disadvantages
Cone crushers are one of the most popular options for aggregate crushing, and they offer some unique advantages over other types of crushing equipment. But, there are also some disadvantages when compared to other equipment.
Today, we're going to take a closer look at the cone crusher advantages and disadvantages so you can decide whether or not this powerful equipment is a good fit for your business.
What is a Cone Crusher?
Cone crushers are compression machines that take in raw materials and reduce them in size by crushing them. A variety of industries rely on these tools, such as the concrete, aggregate, mining, coal, and natural gas industries.
Inside the crusher, a piece of steel, known as the mantle, rotates eccentrically. As the material is loaded into the crusher, the mantle rotates, forcing the material against a stationary piece of steel, known as a bowl.
The machine generates incredible amounts of force, which crush the material as it settles between the mantle and bowl. As the material is crushed, finer particles travel downward inside the machine, where they're further refined until they reach their final size.
The closed side setting determines what the final size of the particles will be and that setting can be adjusted until you've reached the desired material size. Usually, these crushers deliver a 4:1, 5:1, or 6:1 reduction ratio. As you reduce the closed side setting to produce smaller material, you also reduce the capacity of the machine.
Cone crushers are well adapted to handle many different types of material, but they're only able to accept material up to a certain size. Especially large pieces of raw material are generally too large to fit into even the largest cone crushers. That material must be processed before you can load it into a cone crusher.
For businesses that process large pieces of raw material, cone crushers are used as a secondary or tertiary crusher.
The Benefits of Cone Crushers
Cone crushers offer a bunch of benefits that are helpful for practically every industry that relies on this equipment. Many manufacturers turn to a cone crusher because it provides:
● Increased production efficiency
● High crushing ratio
● Less maintenance
● Reliability
● Cost efficiency
Production Efficiency
Cone crushers are built to serve one task exceptionally well, and they're designed with efficiency in mind. These machines can easily be adjusted to increase productivity, allowing businesses to get more done in less time.
High Crushing Ratio
Cone crushers also have a high crushing ratio, and they're able to quickly process raw material to a more uniformly fine size than first stage crushers. As the mantle rotates at high speed, it quickly transforms raw material into smaller particles, which also helps to reduce operational costs.
Easy to Maintain
While a cone crusher may look intimidating, most basic maintenance is quite easy to perform. There aren't many moving parts to worry about, and they rarely break down, provided you stay on top of essential regular maintenance of the machine.
Reliable
Cone crushers tend to last for many years provided you use the machine properly and stay on top of the essential maintenance that's required. Manufacturers spend a great deal of time developing creative ways to protect their equipment from wear, which translates to a longer lifespan for the machine.
Cost-Efficient
Since cone crushers serve one function, it's easy for manufacturers to focus on making them more efficient and cost-effective to run. Today's advanced cone crushers are computer-controlled and carefully optimized to generate the most force while expending the least energy.
While the initial cost of a cone crusher is quite high, their long lifespan allows businesses to absorb that cost over time, which helps make them more cost-efficient. Plus, since there are so few parts required to keep a cone crusher running, there are fewer parts that can break down or wear out over time.
The Disadvantages of Cone Crushers
While there are plenty of useful benefits to these powerful tools, there are also some disadvantages to cone crushers. Depending on how these disadvantages would affect your business, you may find that a different style of crusher is better suited to your needs.
When a business evaluates different crusher types, they tend to shy away from cone crushers because of:
● Size restrictions
● Uniformity concerns
● Material restrictions
Size Restrictions
One of the main disadvantages of cone crushers is that they can only accommodate raw material up to a certain size.
The material you feed into the machine must be pre-dimensioned to the crusher. Most cone crushers have a feed opening size of 5-14", so material that's larger than the maximum size allowable will need a first stage of crushing before they can be fed into a cone crusher.
Final Product Isn't Uniform
Cone crushers do an excellent job of providing finished material that's relatively homogenous. But, if you need your final product to be completely uniform, a cone crusher isn't going to be able to provide that. Many material specs require complete uniformity, and if that's true in your industry, you'll need to look towards a different crusher.
Can't Handle Every Type of Material
Cone crushers are ideal for a wide variety of materials, but the nature of their design means that particular materials can jam the crusher. A cone crusher makes quick work of medium to hard materials, but it doesn't do well with softer ones. In particular, moist or viscous materials such as clay aren't suitable for this style of machine.
Selecting a Crusher
Depending on the needs of your business, there are a few key things to consider before you select the best crusher for your needs. The primary areas to look at include:
● Material hardness/abrasiveness
● Loading size
● Finished material size
● Throughput
The first thing to consider is the type of material you'll be crushing. Specifically, how hard and abrasive that material is. Businesses that crush extremely hard and rough materials will need a machine that can provide the power they need to get the job done.
The loading size is also critical, as you won't be able to crush what you can't fit in the machine. Consider the largest possible material you'll be crushing, and ensure that the crusher you choose can accommodate it.
The finished size of the material is also quite important, as many industries rely on a closely toleranced and uniform final product.
Finally, a crusher's throughput or the amount of material it can process must be considered. Throughput is measured in tons per hour, and machines with a larger throughput will be able to process higher amounts of material in the same amount of time.
Cone Crusher vs. Jaw Crusher
When it comes to aggregate crushing machines, there are several different options available, each designed to meet the unique needs of the businesses they serve.
The two most popular crushers are cone crushers and jaw crushers, and they're the go-to tools for a variety of different industries. Today, we're going to delve deeper into these powerful machines to help you decide between cone crusher vs. jaw crusher for your business.
What Are Aggregate Crushers?
A surprisingly vast array of industries use aggregate crushers. From building materials to antacids, there's a strong chance that an aggregate crusher was used to refine raw materials into the finished product you recognize.
Limestone, sand and gravel are three of the most common materials associated with aggregate crushers, and they are vital ingredients in building materials like concrete, asphalt and cement. There also are many specialty products that these raw materials are used to make. Some popular rock crusher applications include:
● Sandstone
● Limestone
● Sand and gravel
● Gypsum
● Frac sand
● Roof shingles
● Shale
● Chicken Grit
● Ice Grit
● MSHA Rock Dust
● Animal feed supplements
● Shells
What is a Jaw Crusher?
Jaw crushers are a compression crusher that uses a set of jaws to crush aggregate materials. This machine features a fixed jaw and a moving jaw, oriented in a V position. Once you load material into the crusher, the movable jaw pushes material into the fixed jaw until it's crushed to the desired size.
A variety of moving parts allows the movable jaw to crush material, including the flywheel, toggle plates, eccentric shaft, motor and pitman. Working together, these parts generate an incredibly powerful force that allows the movable jaw to crush material.
Once the jaws of the machine process the material, it exits through a discharge opening at the bottom of the machine. Adjustments to the discharge opening allow the user to control the final size of the crushed material.
Jaw crushers are a primary tool for material reduction, and rock quarries, as well as the sand, gravel, mining, construction, metallurgy and chemical industries, use jaw crushers to refine the material.
The most common jaw crushers are the eccentric overhead jaw and double toggle jaw crushers. Models are available in stationary, wheeled and track-mounted configurations.
Advantages of a Jaw Crusher
Jaw crushers offer a few inherent advantages that make them popular across many different industries.
We can apply these crushers to an incredibly broad range of materials, and they're compact compared to other types of crushers. Their small size makes them easier and less costly to install, and there is less infrastructure involved with the installation. These characteristics help to reduce site costs, making jaw crushers a cost-effective option for aggregate material crushing.
What is a Cone Crusher?
Similar to jaw crushers, cone crushers are another compression crusher that aggregate, concrete, mining, natural gas extraction and coal industries use.

Inside a cone crusher, two parts are responsible for the magic that happens inside. A piece of steel called the mantle rotates within the machine, crushing material against a stationary piece known as the bowl. As the material passes through the crusher, the distance between the mantle and bowl gets smaller, breaking the material smaller in the process.
Depending on the size you'd like the finished material to be, the gap setting between the mantle and the bowl can be increased or decreased.
Some cone crushers use bushings while others use bearings. Bearing cone crushers tend to run cooler and are more efficient than bushing crushers, and they allow the user to apply more horsepower during crushing without generating excessive heat. Bushing cones create more heat and require lots of lubricating oil and more active cooling systems. However, they're more affordable than bearing crushers.
Advantages of a Cone Crusher
Cone crushers offer a wide range of processing capacity, they're efficient, and they produce a final product of a uniform size. When materials enter the crushing chamber, they're discharged automatically after crushing is complete. Plus, cone crushers can be controlled remotely, helping to reduce work site dangers in the process.
Cone Crusher vs. Jaw Crusher: Key Differences
While companies use both machines for crushing raw materials, several vital differences may make one type of crusher better than the other for your application.
How They Work
The primary difference between the two is how they crush material.
With jaw crushers, the mobile jaw crushes material against the fixed jaw by extrusion. As the movable jaw moves further from the fixed jaw, crushed material slides down the crushing chamber where it's discharged.
With cone crushers, a transmission shaft rotates the mantle, crushing material against the bowl. As the material is broken, it passes down the sides of the machine until it's small enough to be discharged.
Material Handling
Some crushers are better adapted to handling certain materials. For example, a jaw crusher can make quick work of viscous materials that contain a lot of moisture. But, viscous materials will cause a cone crusher to jam.
Further, how much material the machine can handle differs. With a jaw crusher, the material must be evenly fed into the crusher, and the amount of material inside the crusher cannot exceed 2/3rd of the crushing chamber height.
With a cone crusher, the material does not need to be fed as carefully, and material can be fed directly into the machine until it's full.
Cost
Cost is a significant difference between these two styles of crushers.
Cone crushers are more expensive than jaw crushers at the outset, and they're also more costly to maintain since the installation and maintenance of these crushers is more involved and time-consuming than that of a jaw crusher.
Application
While these two machines technically serve the same purpose, they are typically used at different stages of production. Jaw crushers are considered a primary machine, used for crushing raw materials into smaller and more manageable sizes.
Cone crushers are usually used in the next stage of production, where the material from the jaw crusher is refined to an even smaller size.
How to Adjust a Cone Crusher
Cone crushers are one of the most versatile pieces of crushing equipment available, and you'll find cone crushers across a variety of different industries, from mining to concrete to recycling and more.
Cone crushers are relatively simple machines that are easy to understand and operate. But, to maximize production while also reducing energy costs, careful adjustments are necessary from time to time.
Today, we're going to take a closer look at how to adjust a cone crusher and learn about some helpful tips that can help keep your cone crusher running in top shape.
Understanding the Cone Crusher
The first step in learning how to adjust a cone crusher is understanding the principles in place that allow the cone crusher to do its job.
Based on the diagram above, we can identify the main parts of a cone crusher: the feed opening, the concaves, the mantle and the sizing gap.
First, the material enters the feed opening, where it can enter the crushing chamber. Inside the machine, a motor drives the cone or mantle. The mantle rotates eccentrically, which is to say that it doesn't move in a circle. As the mantle moves, it swings off-axis slightly, which allows the crushing action to take place.
As the mantle rotates, it crushes material between the mantle and the concave, which causes it to break into smaller pieces. These smaller pieces can travel further down the crushing chamber, where they can be crushed as many times as is necessary to reach their final size. Once the final size is reached, the material discharges from the machine where it can be collected for final processing.
The last piece of this puzzle is the sizing gap. Since the mantle rotates eccentrically, there are always two different sides at play: the open side, which represents the greatest gap between the mantle and the concave, and the closed side, which is the smallest gap.
The distance between the mantle and the side is the primary area where cone crushers can be adjusted. These settings are known as the OSS (open side setting) and CSS (closed side setting.)
The opening on the open side determines the maximum particle size of the finished product. The closed side not only determines the minimum particle size of the finished product, but also how much material the crusher can accommodate, and how much energy it requires to crush it.
Adjusting a Cone Crusher
Depending on the type of machine you have, it can either be adjusted by the top or bottom.
Many cone crushers, like those manufactured by Sandvik, allow for adjustment at the bottom of the crusher. A hydraulic piston allows the user to make adjustments to the closed side setting. Depending on the type of material you're working with, the closed side setting will need to be adjusted to optimize particle size, loading and the amount of energy required to crush the load.
This style of crusher also allows you to adjust the throw of the mantle. This setting relates to how far the mantle spins off its axis with each rotation. This adjustment can be made through a bushing located at the top of the machine.
By optimizing the throw of the mantle, you'll be able to ensure a more uniform particle size, while also ensuring that the mantle makes impact with the raw material at the point of maximum impact. This adjustment is critical if the goal is to reduce the amount of energy it requires to process a load.
Other styles of cone crusher, like those manufactured by Cedarapids and KPI-JCI, allow for closed side setting adjustments at the top of the machine. With these crushers, this adjustment is made by tightening or loosening the bonnet at the top of the crusher.
If you're an operator who isn't sure which style of crusher is best for your business, you'll want to spend plenty of time considering the maintenance implications of different crushers. Crushers that adjust from the bottom, like the Sandvik example above, tend to have less moving parts and require less maintenance and repair than top-adjusting crushers.
Tips for Getting the Most Out of Your Cone Crusher
While careful adjustments are critical to achieving optimal efficiency, adjustments are only one piece of the puzzle. There are also some simple things you can do to help your crusher perform at an optimal level.
Keep Your CSS Consistent
A consistent output requires consistent CSS settings. If this setting is thrown out of whack, the result will be less production and a final product that is larger or less uniform than intended. Plus, an oversized product can lead to other issues within the circuit flow.
Keep a Consistent Feed Level
How material is fed into the crusher has a notable effect on the shape and quality of the final product. If the crusher is allowed to operate at different feed levels throughout a shift, you'll lose productivity and the quality of your finished product will suffer, as well.
Keeping a consistent feed ensures product uniformity while also providing consistent and reliable production throughout a shift.
Direct the Feed into the Crusher's Center
Ensuring the feed level is even and consistent throughout the crusher is another way you can maximize productivity and improve the appearance of the final product. The feed should be directed to the center of the crusher, and the crusher will do the work of distributing the feed properly.
If the feed is directed to one side or the other, the resulting product will be oversized and inconsistent, and the crusher's throughput will be reduced.
Know the Limits of the Machine
Every crusher has some inherent design limitations that can't be exceeded.
● Volume limit
● Horsepower limit
● Crushing force limit
Every crusher cavity has a volume limit that must be adhered to maximize throughput. Exceeding this volume will have implications for your final product size, and it will also reduce the productivity of your machine. If your feed material is overflowing out of the top of the feed opening, you've exceeded your volume limit.
Each crusher is optimized to work at a specific maximum power draw. If you're feeding too much material into the crusher, you'll end up exceeding the horsepower limit, which means that your machine is using power above what it's rated for, which can lead to premature wear and burn out.
The final limit to consider is the crushing force limit. When the feed rate is increased, so is the amount of crushing force that must be generated to break the material. You'll know you've exceeded the crushing force of your machine if there is play in your adjustment ring.
If you notice it bouncing, bumping or jumping on top of the mainframe, the crushing force limit has been exceeded.
Cone Crusher Diagram
Crushing equipment is the lifeblood of a variety of different industries. From mining to concrete to rock quarries and more, crushing equipment is what allows companies to refine raw materials into a finished product that's ready to go to market.
Large enterprises usually deploy a variety of different pieces of crushing equipment, and the cone crusher is one of the most critical tools they use. But, how exactly do these massive machines work? While they may look intimidating at first, it's easy to understand the inner workings of this equipment with a little help from a cone crusher diagram.
What is a Cone Crusher?
Crushers come in a variety of different styles and configurations, including jaw crushers, impact crushers and cone crushers.
Cone crushers are a compression machine that takes in raw material and compresses it between a moving piece of metal and a stationary piece of metal. As the material breaks, the smaller particles travel downward inside the machine where they can enter the next stage of crushing or exit the machine completely for final processing.
The Elements of a Cone Crusher
At face value, cone crushers look like an intimidating piece of equipment. Thankfully, they aren't nearly as difficult to understand as you may think. Cone crushers are quite a simple machine, and once you know the different parts of the device, it becomes much easier to understand how they work.
Feed Opening
Looking at the cone crusher diagram above, the feed opening is the first aspect of the machine. The feed opening is where the raw material feeds into the crusher. Even the largest cone crushers are limited by the size of their feed opening, as they can only accommodate pieces of rock or substrate that will fit inside the machine.
For this reason, cone crushers companies often use cone crushers as a secondary or tertiary stage of crushing. A first stage machine breaks the enormous pieces of material, and then the smaller pieces of rock or substrate can be loaded into the feed opening where they can be further refined until they've reached their final size.
Concave
The next piece of a cone crusher is the concave. As the name entails, the concave is a steel sleeve that curves inward inside the crusher. As the crusher runs, it crushes the material against the sides of the concave, where it's broken into smaller pieces.
As the rocks get smaller, they're able to slide further down the concave, where they'll be crushed further until they've reached their final size.
Mantle
The mantle is where the magic happens inside of a cone crusher. The mantle is made from steel or iron, and it's shaped similarly to a lampshade. The end of the mantle connects to the crusher's motor, and when the machine is on the mantle rotates, crushing the material in the process.
It's important to note that the mantle rotates eccentrically. In layman's terms, this means that the mantle does not turn in a perfect circle. Instead, as it rotates, the mantle swings slightly to one side or the other.
This action allows the mantle to generate the crushing force necessary to crush material on the side it swings closest to, which smaller pieces of material that have already been broken are able to slide down to the next stage of crushing or exit the machine completely for final processing.
The Sides of the Crusher (OSS & CSS)
As the mantle rotates within the crusher, there is always a side with a wider opening and a side with a smaller one. These sides of the crusher are referred to as OSS (open side setting) or CSS (closed side setting.)
How the user configures these settings will determine the final size of your product. The OSS represents the largest distance between the concave and the mantle, and this side determines the largest size of outgoing particles. The opposite is true with the CSS. Since the opening on this side is much smaller, it represents the final crushing zone inside the machine.
The closed side setting also is critical in determining the size of your final product, as well as how much material the crusher can accommodate, and how much energy it requires to crush the material.
Companies spend a great deal of time engineering the optimal settings for their crushers. Factors like material composition, hardness and particle size can have a profound effect on the optimal settings for the crusher.
When the side settings of a cone crusher are optimized, it allows the user to increase productivity, reduce energy costs and produce a more uniform product. For large operations, these processes are usually handled by a full-time engineer whose job is to keep the crushers running as efficiently and productively as possible.
Motor
The unsung hero of the entire machine, the motor is what drives the mantle and allows crushing to take place. These motors are incredibly powerful and capable of generating a massive amount of power that material crushing requires.
Cone crushers come in all sizes, so the same is true for their motors. Commercial cone crushers that are used in the mining, aggregate and building material industries commonly have large engines with 1,000 horsepower or more. These large motors can generate the power necessary to allow commercial cone crushers to do their job.
Feeders
A feeder is an optional piece of equipment that large companies use in concert with a cone crusher in large commercial settings, such as rock quarries. A feeder works like a conveyor belt. The raw material is loaded onto the feeder, and the feeder moves the material along the conveyor belt, where it can then be loaded into the feed opening for crushing.
Final Word
After taking a closer look at the cone crusher diagram above, you should now have a much better idea of the inner workings of these powerful machines. While their composition may be simple, cone crushers act as the backbone for a variety of different industries.